SAGE
FLY RODS FACTORY TOUR - 2003
In the late
fall of 2003, I was lucky enough to have a free morning while
visiting relatives in the Seattle region. Being one of the larger
Sage dealers does have its benefits, and my wife, father-in-law
and I were able to wrangle a tour of the Sage rod production
facility on Bainbridge Island, WA. They even let me take some
photos of some parts of the operations.
If
you want to see a larger version of any photo - simply click
on it and it will open in a separate window.
This
"sandwich" will become racks of Sage Fly Rods. This
is a stack of cut composite laminate material, labelled for
the rod model and section. This will be wrapped around the forming
mandrel under heat and pressure. Those with sharp eyes will
see that this is the butt section for the Saltwater Series 990-4
Xi2 rods, introduced in the fall of 2003. These have been precisely
trimmed and layered from huge rolls of different composite materials.
This sandwich
of varied composites will be separated into the proper set of
layers before rolling onto the mandrel.
The
secret nerve center of the actual Sage construction facility.
These metal mandrels shown in the forward bins will be used
to form individual sections of fly rods. The taper of these
create the individual sections of what will become a Sage fly
rod. The actual taper of the mandrel determines how the section
will be formed - it is critical to the final action of the rod.
Beyond this
is a rack of inidividual blank sections which have been rolled
and approved, labeled and ready for the next steps in the process.
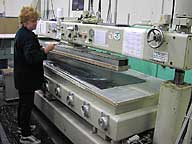
Two ends of the forming process. (The machine "rolls"
pretty quickly, and with the lighting, I couldn't get a good
clean shot of it in action.) The composite laminate is tacked
down precisely on one end of the material, and then rolled around
the mandrel under heat and pressure using the machinerey made
for Sage. The operator carefully aligns the mandrel on the edge
of the laminate material, then presses the "GO" button.
The entire horizontal arm comes down, putting the heated press
into direct contact with the material. It then sweeps through
a predetermined arc, putting tremendous pressure and heat onto
the section as it gets rolled around the mandrel. At the end
of the arc, the arm is released and swings back to the original
postiion. And out of the "oven" pops a newly formed
rod section, with the mandrel in the middle.
The
formed sections are stored in a vertical rack before the first
of many quality control stations. Note the gauge - it gives
a constant readout of temperature and humidity so that the press
operator can monitor her machine temperature during the day.
Next, the
mandrel is popped out, leaving the tapered graphite composite
section ready for the next steps. The unfinished sections are
allowed to cool slightly before moving on.
Once
cooled, the wrappin layer is peeled off and the blank is sanded
smooth. This is an extremely critical step trusted to a very
few employees, as removing too much of the finish can sacrifice
rod strength. The technician who accomplished this step had
been doing it for years.
After this
step, the blanks go through another QC step. Then they go through
the heat treating step. This proprietary process was OFF-LIMITS
to our cameras. I guess I could've put a picture or two from
the rest of our vacation....
After
heat-treating (a 24-hour long process), cooling and another
trip through the QC process, the rod blanks receive a color
(dependiing upon their series finish) and protective coating.
This is achieved by manually dipping the blank into a vat with
a specialized squeegee system - the layer of epoxy must be super-thin
so as not to add excess wieght. It also must be entirely even
over the blank or it is failed on Quality Control. It takes
a steady hand to work the blank through this step, but the results
are impressive (OK, MUCH more impressive than this photo would
suggest...) The coated blanks are then are hung to dry. Again,
watchful eyes have passed the blanks through this process, weeding
out any that don't meet the stringent requirements.
This rack
is drying blanks will move next to the finishing stations.
Every
one of the premium rods you see here has received a set of individual
cork rings, which were then formed to the half-wells grip as
shown. I was surpised to find that Sage uses the individual
rings, rather than preformed grips.
I tried
to get a shot of the forming, but it's in an enclosed (and heavily
ventilated) room - cork flying all over the place! Still, this
impressive view of aisles and aisles of top quality rods with
sparkly new reel seats is one of my favorite. I wonder which
ones will be ours?
After
that, every Sage rod receives its label via a silkscreen process
- you are looking at the silkscreen for the RPLXi series (now
merely a historical remnant). I always thought this was a decal
- but was corrected.
There is
a tremendously tall rack of silkscreens, covering every rod
model made by Sage - pretty impressive when you see the variety.
But, that's why we like to support Sage - they have such a breadth
of actions and sizes to offer.
There
is no better way to finish a rod than at the hands of an experienced
guide wrapper. The people doing this work (there were more than
a half dozen stations going at full speed) had been doing this
for years, and the crisp uniformity of their quality work is
on every finished rod. The speed with which they were able to
work is iimpressive, but the absolute precision of their craft
is even more so.
After another
QC check, the rods proceed to final finishing - a separate climate-controlled
room for the epoxy finishing step - again, no photos allowed.
But, they
did let us look through the windows, and we could see hundreds
of rods rolling slowly as the epoxy hardened. Numerous technicians
in clean-suits were continually checking quality under the bright
lighting. After the rods have finished, they receive the final
tests to make sure that they are cosmetically perfect and functionally
correct. Only then do they get to take the final "march
down the aisle."
Finished
and checked Sage fly rods get matched to the proper color-coded
cloth bags, are scanned out by serial number and matched to
the appropriate warranty card, and are nearly ready to go out
to the happy dealers (like us!). The final packing takes place
up the street at a different facility - where the rods are matched
to the proper tube and boxed for shipment to the dealer.
Even through
I've seen other rod manufacturing facilities before, it is always
suprising to see just how many steps it takes to make a premium
fly rod. At every step of the construction, the blanks run a
gauntlet of Quality Control steps - and those that don't meet
th rigid and specific requirements are weeded out. The commitment
to maintain such high production standards sets Sage apart -
they really care about what leaves their production facility.
It's also
impressive how many hands-on steps there are - this isn't really
something you can leave to for the machines to work out. Despite
the computers, equipment, and high-tech composites which they
use, there is a sense of "feel" in the production.
I suppose you could probably cut that down a bit, and maybe
save some money, but the high-quality results of the Sage production
really speaks for itself. It was an impressive tour!
Thanks again
to Sage for putting up with our intrusion, and for taking the
time to show us around the production facility and answer all
of our questions!
|